How 3D Printing is Influencing Concrete Mixer Component Manufacturing
- wangamy263
- Apr 28
- 3 min read
3D printing is revolutionizing many industries, including concrete mixer component manufacturing. This technology impacts the production of self loading, mobile, and small concrete mixers. Understanding these changes provides valuable insights for customers and manufacturers alike.
The Rise of 3D Printing in Manufacturing
3D printing, or additive manufacturing, builds objects layer by layer. This method differs from traditional subtractive manufacturing, which removes material. Its precise nature offers numerous benefits for concrete mixer component production.
Manufacturers now use 3D printing to create complex parts. This capability simplifies the production process and reduces costs. The technology enhances design flexibility, allowing for rapid prototyping and innovation.
Efficiency in production leads to faster turnaround times. Manufacturers meet increasing demands without compromising quality. These improvements benefit customers seeking reliable and efficient concrete mixers.

Advantages of 3D Printing for Concrete Mixers
3D printing brings specific advantages to concrete mixer manufacturing. One significant benefit is reduced material waste. Traditional methods often require excess material, whereas 3D printing uses only what is necessary.
Customization becomes easier with 3D printing. Manufacturers tailor components to specific mixer types, such as the self loading concrete mixer. This adaptability enhances mixer performance and customer satisfaction.
Durability is another advantage. 3D printed components often exhibit superior strength and resilience. These qualities ensure long-lasting mixers that withstand demanding construction environments.
Impact on Self Loading Concrete Mixers
Self loading concrete mixers benefit greatly from 3D printing. The technology allows for precise component design and construction. This precision improves the efficiency and reliability of automated loading systems.
3D printing also facilitates lightweight component production. Lighter parts enhance mixer mobility and reduce fuel consumption. These improvements contribute to cost savings and environmental benefits.
Manufacturers leverage 3D printing for rapid prototyping. This flexibility lets them test new designs and innovations quickly. It fosters continuous improvement in self loading mixer technology.
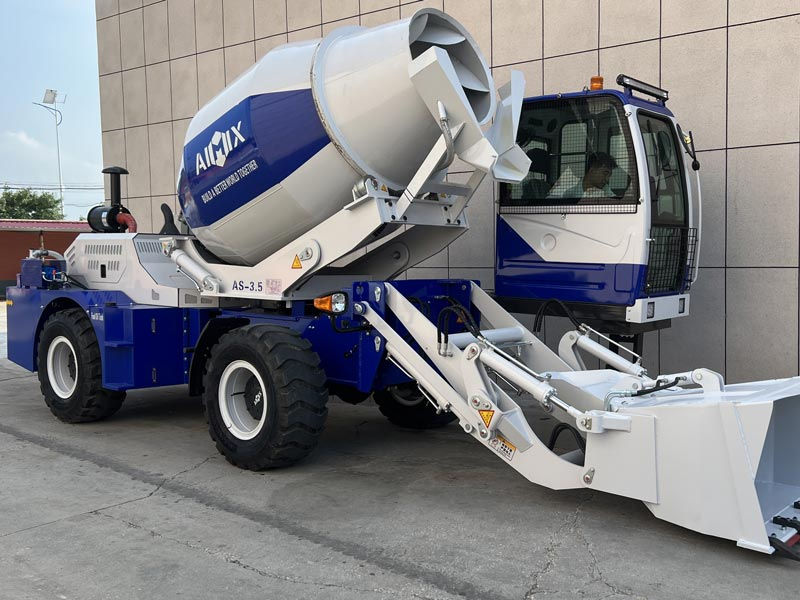
Influence on Mobile Concrete Mixers
Mobile concrete mixers gain unique advantages from 3D printing. Their components require adaptability and strength. 3D printing delivers these qualities, ensuring mixers perform optimally in diverse environments.
The technology enables intricate design features. These designs enhance mobile concrete mixer maneuverability and efficiency. Operators benefit from improved control and ease of use.
3D printing supports sustainable practices. Mobile mixers often serve urban areas with strict environmental standards. Reduced waste and energy consumption align with these sustainability goals.
Small Concrete Mixers and 3D Printing
Small concrete mixers also benefit from 3D printing innovations. Precision in component production ensures accurate mixing and minimal waste. This precision directly impacts cost savings and efficiency.
Customization is key for small concrete mixer machine. 3D printing allows manufacturers to tailor components to specific project needs. This flexibility enhances mixer versatility and application.
Durability remains a priority for small mixers. 3D printed parts withstand wear and tear, ensuring long-term reliability. These resilient components enhance customer trust and satisfaction.
Future Prospects and Innovations
The future of 3D printing in concrete mixer manufacturing looks promising. Continued advancements will likely enhance component design and strength. These improvements will further optimize mixer performance.
Manufacturers may explore new materials for 3D printing. These materials could offer enhanced durability and environmental benefits. Innovations in material science will drive future developments.
Increased collaboration between manufacturers and technology experts will foster innovation. Sharing knowledge and resources accelerates progress and benefits all stakeholders.
Conclusion
3D printing is transforming concrete mixer component manufacturing. Its influence on self loading, mobile, and small mixers is profound and valuable.
The technology offers numerous advantages, including reduced waste and enhanced customization. These benefits improve mixer performance and customer satisfaction.
Understanding 3D printing's impact helps customers choose the right mixers for their needs. Manufacturers continue to explore new possibilities, ensuring ongoing improvements in mixer technologies.
As 3D printing evolves, its role in concrete mixer manufacturing will expand. Embracing this technology ensures a successful and sustainable future in construction equipment production.
Comments